Mastering Flange Bolt Torque Calculation
Ever wondered how those massive industrial flanges stay sealed under immense pressure? The secret lies in precise flange bolt torque calculation. Getting this right is crucial for preventing leaks, ensuring safety, and maximizing the lifespan of your equipment. Let's dive deep into the world of flange bolt torque and discover how to achieve perfect connections every time.
Calculating the correct torque for flange bolts isn't just about tightening them as hard as possible. It's a precise process that balances the clamping force needed to create a seal with the risk of over-tightening and damaging the bolts or the flange itself. An improperly torqued flange can lead to catastrophic failures, leaks, and costly downtime. Understanding the fundamentals of torque calculation empowers you to prevent these issues and maintain the integrity of your systems.
The history of flange bolt torque calculation is intertwined with the development of bolted joints and pressure vessels. As industries like oil and gas, chemical processing, and power generation evolved, so did the need for standardized methods of ensuring safe and reliable flange connections. Over time, various formulas and guidelines emerged, incorporating factors like bolt material, size, and lubricant to refine torque calculations and improve joint integrity.
The importance of accurate flange bolt torque cannot be overstated. In high-pressure applications, even a slight miscalculation can have serious consequences. A leak can release hazardous materials, cause environmental damage, and lead to costly shutdowns. Over-tightening, on the other hand, can damage bolts, warp flanges, and create stress points that ultimately weaken the entire assembly.
One of the main issues related to flange bolt torque calculation is the variability of factors affecting the final result. Lubrication, bolt material, gasket type, and even temperature can influence the friction within the joint and affect the required torque. Therefore, relying solely on generic torque values can be misleading. A thorough understanding of these variables and how they interact is essential for achieving optimal results.
A key concept in flange bolt torque calculation is the K-factor, which represents the nut factor or friction coefficient. This factor accounts for the friction between the nut and bolt threads, as well as under the nut's bearing surface. Determining the appropriate K-factor is crucial for accurate torque calculations. You can find K-factor values in engineering handbooks and manufacturer specifications.
One simple example is using the formula T = KDF, where T represents torque, K is the nut factor, D is the bolt diameter, and F is the desired bolt load. Let's say you have a 1-inch diameter bolt and a desired bolt load of 20,000 lbs, with a K-factor of 0.2. The required torque would be T = 0.2 * 1 * 20,000 = 4,000 lb-in.
Accurately calculating flange bolt torque provides several benefits. First, it ensures a leak-free seal, preventing hazardous material releases and maintaining system integrity. Second, it optimizes bolt load, minimizing the risk of bolt failure and maximizing the lifespan of the flange connection. Third, it reduces maintenance costs by preventing leaks and equipment damage, leading to increased uptime and productivity.
A step-by-step guide to calculating flange bolt torque typically involves identifying the bolt material and size, determining the desired bolt load based on the application and gasket type, selecting the appropriate K-factor, and then applying the torque formula. Remember to consult relevant standards and manufacturer recommendations for specific guidance.
Advantages and Disadvantages of Precise Torque Calculation
Advantages | Disadvantages |
---|---|
Leak-free connections | Requires precise measurements |
Increased safety | Can be time-consuming |
Extended equipment life | Requires specialized tools |
Best practices include using calibrated torque wrenches, lubricating bolt threads and nut bearing surfaces, tightening bolts in a specific sequence, and regularly inspecting and re-torquing flange connections.
Frequently Asked Questions:
1. What is flange bolt torque? Torque is the rotational force applied to a bolt.
2. Why is it important to calculate flange bolt torque? To ensure a secure, leak-free connection.
3. What factors affect flange bolt torque? Bolt size, material, lubrication, and gasket type.
4. What are the consequences of incorrect torque? Leaks, bolt failures, and flange damage.
5. What tools are used for torque calculation? Torque wrenches and calculators.
6. How often should flanges be inspected? Regularly, based on operating conditions.
7. Where can I find torque specifications? Manufacturer's guidelines and industry standards.
8. What is the K-factor? A coefficient representing friction in the bolted joint.
In conclusion, mastering the art of flange bolt torque calculation is essential for anyone working with bolted flange connections. From preventing leaks and ensuring safety to maximizing equipment lifespan and minimizing downtime, the benefits are undeniable. By understanding the factors that influence torque, following best practices, and staying informed about industry standards, you can ensure reliable and efficient operation of your systems. Take the time to learn and apply these principles – your equipment and your bottom line will thank you. Invest in proper training and tools, and don't hesitate to consult with experts when needed. A small investment in accurate torque calculation can save you from significant headaches and expenses down the road. Start implementing these best practices today and ensure the integrity and longevity of your flange connections.
Mastering your whatsapp profile picture a complete guide
Taming the beast the g80 m3 as your everyday companion
Dive into sherwin williams stunning blue green hues


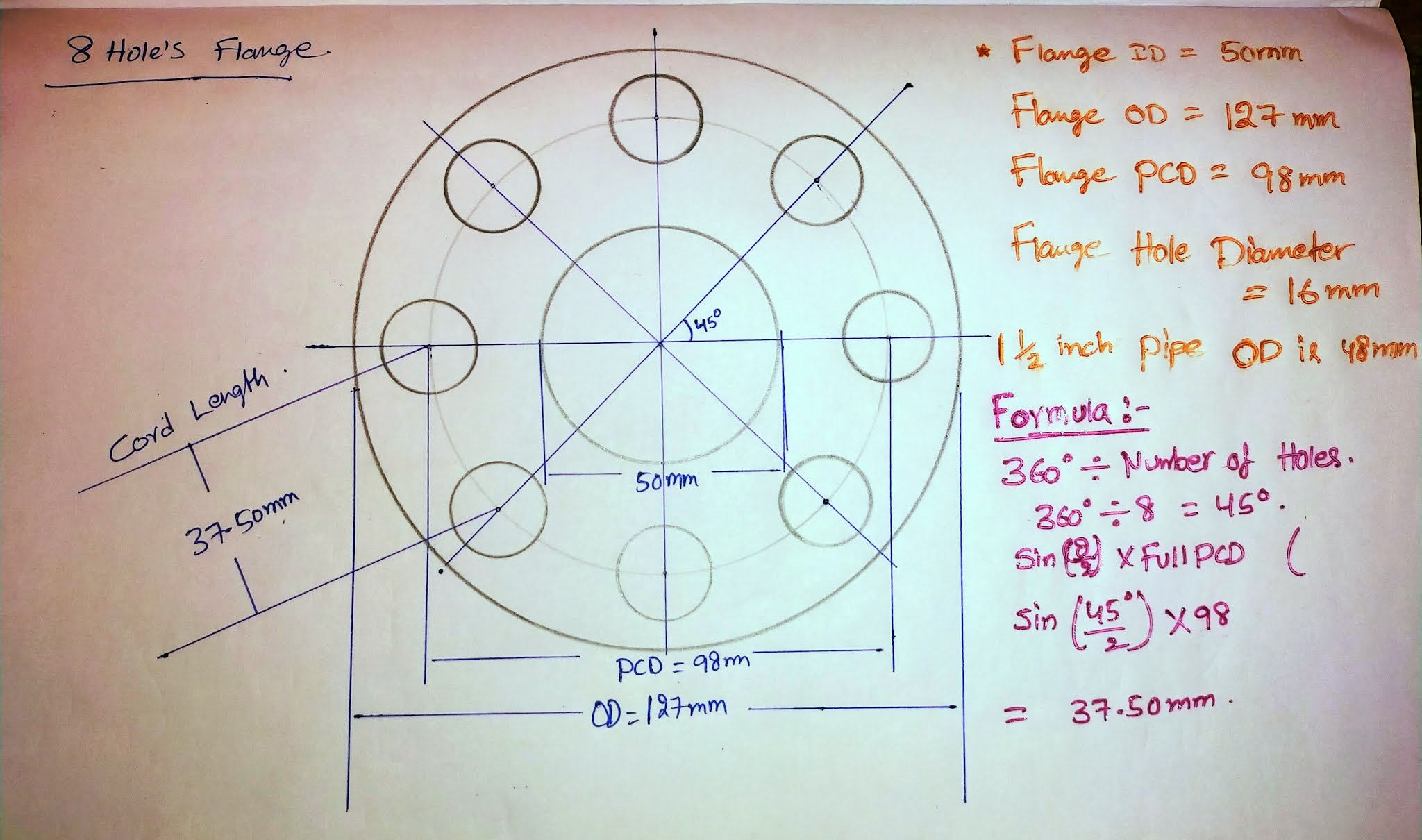










